As you design a manufacturing space, building, or site, you may want to cut a corner here or there to save time or money, but there are some that you should think twice about. “But I don’t have an unlimited budget or all the time in the world!” We know - but hear us out first.
The following are six design decisions you will make as you plan your manufacturing building project and why you should consider giving them a little extra thought.
1. Site Management.
Site management focuses on the flow of traffic around the outside of the building. Next to determining how much space a building needs, this is the second-most important step to consider.
2. Getting It Right vs. Getting It Cheap.
Indeed, you have to be respectful and mindful of a budget; however, if you start with a hard, low amount, you might as well be saying, “Let's just build the cheapest thing we can have, no matter what,” and we know that isn’t your real end-goal for your project. You want a building that will last, that you can be proud of, and your employees will be happy to occupy.
3. Air Conditioning.
It may go without saying, but you’d be surprised how many people don’t understand this concept. Air conditioning is now a standard amenity in many modern-day manufacturing facilities, so if you cut this corner in the name of budget, you may not be able to find the labor you need or keep them around.
4. Natural Lighting.
When energy conservation became a significant factor in operational costs and code restrictions, the paradigm shifted to spaces with little or, in some cases, zero natural light. However, we can now design spaces that meet or exceed code, are energy efficient, and provide natural light!
5. Employee Enrichment Areas.
An employer needs to offer spaces for employees to take breaks or briefly step away from their workspaces. A mental time-out in a clean room with access to a kitchen and/or vending equipment can allow employees to recharge and prepare for the remainder of their workday.
6. Design for the Future.
A building should be designed so it’s easily expandable and major elements such as loading docks, utility services, and building entrances can remain intact. It is also important to design site elements like stormwater management, parking areas that are easily expandable with future expansions, and more.
Continue reading to learn more about these decisions and why you won’t want to cut these corners or go the cheapest route. Spoiler: It all helps your future budget, employees, and building.
Don’t Cut These Corners for Your Timeline
It can be tricky to get projects done on time; however, to know which corners NOT to cut while trying to keep pace with your project timeline is key.
1. Site Management
Have you ever pulled into a parking stall and thought to yourself that it seemed like a tight squeeze? Or have you ever backed out of a parking stall and had to switch from drive to reverse several times just to get out of it? If so, you’ve been a victim of a cut corner.
Site planning should not be a secondary thought in the process of constructing or expanding a new building. Although cutting this corner or skipping this step happens more often than it should.
- Where is the most optimal location for the building on the site?
- What should the flow of the exterior of the building look like (people/vehicles/etc.)?
- Where is the most efficient location for the loading docks?
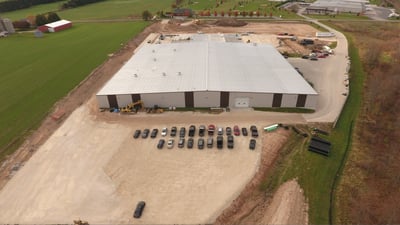
These questions and much more will come up no matter what, but what we want to tell you is that this is where your focus should begin. Make sure the answers to these questions are thoroughly thought out ahead of time and are never afterthoughts.
The site should be designed efficiently; otherwise, significant money can be wasted. On average, the following site work can account for 5 - 15% of a project’s total cost.
- Excavation
- Building utilities
- Asphalt paving
- Stormwater management
- Landscaping
Saving money on the project budget is key, but so is creating a safe environment. Safety is equally important on the outside of the building as it is on the inside. It’s critical to consider how cars and trucks will interact on the site. To do this, keep loading docks separate from parking areas and pedestrian traffic protected or properly guarded against vehicle traffic. It’s also vital to properly survey the site early to identify potential barriers like easements, wetlands, or underground utilities.
What Can Go Wrong?
Besides the potentially wasted money from inefficient design, the biggest complication are the effects that snowball from a poorly designed site. This includes water that doesn’t drain properly (endless problems in your future) or a traffic flow pattern that puts employees’ safety at risk.
How Can A.C.E. Help?
A.C.E. offers a broad range of in-house surveying and land development services to Northeastern Wisconsin. We provide professional, accurate, client-focused land surveying services of the highest quality to our clients. We can handle the site design ourselves or lead the design effort with a trusted civil engineering partner. Click here to learn more about A.C.E.’s surveying services.
2. Value Getting It Right vs. Getting It Cheap
The two common denominators in construction are square footage and cost; thus, people tend to fixate on these numbers and forget everything else. They ask, “How big and how much?” but there are other numerators (number of parts) that are involved.
The following questions beg you to think about what it will take to get your project ‘right:’
- What are you going to put inside of your building?
- What amenities are there going to be for the employees?
Where do I begin? If there is anything else to focus on other than budget, I would recommend focusing on your vision or non-negotiable items. Consider the safety and comfort of your most valued asset - your employees! What can you do to make your employees more comfortable and enjoy their working environment without breaking the bank?
Have a realistic budget established early. It’s easy to fall into the trap of having champagne taste on a beer budget. Being in tune with a solid budget early will allow you to plan accordingly with capital planning and early discussions with lenders.
What Can Go Wrong?
If you do not value getting the project done right the first time around, you may have to rework your plans; this equates to wasted time and even worse, wasted opportunity. The sooner your project is constructed, the sooner you can fulfill customer orders, increase production capacity, and make more money.
How Can A.C.E. Help?
Our preconstruction process always begins with a preliminary feasibility budget to help owners identify if a project is viable or not. Our process has been proven time and again to help our clients effectively plan their construction projects from the beginning.
Don’t Cut These Corners for Your Employees
In the name of employee retention, in the world that we live in today, the companies that are most successful in attracting employees are the ones that provide amenities that the other companies don’t.
We’re not saying your facility has to look like Google’s headquarters; let’s just start with some basics such as air conditioning inside manufacturing facilities. Years ago, that wasn't heard of. But now it’s a strongly considered amenity to attract and retain employees.
3. Air Conditioning
Developers and building project managers have to ask themselves the right questions in today’s ultra-competitive work environment, such as, “How much more productive will an employee be if they are comfortable in their conditions?” Equally important as it is to ask the right questions is to find the answers and follow through with them.
As such, air conditioning is now a standard amenity in many modern-day manufacturing facilities, so if you cut this corner in the name of budget, you may have a harder time finding the labor you need or to keep employees around.
What Can Go Wrong?
What are the adverse side effects of cutting this corner and not including A/C in your manufacturing facility? Your employees may find themselves fatigued a lot more often or sooner than in a facility with air conditioning. Fatigue can lead to a higher risk of errors or even rework. Additionally, foregoing A/C can lead to losing talent to other manufacturers that do have climate-controlled environments.
How Can A.C.E. Help?
A.C.E. Building Service provides efficient designs for buildings to work in conjunction with climate-controlled environments. Designs such as the placement and location of windows that allow natural light but deny solar heat gain. Efficient building envelope design, such as eliminating thermal short-circuits, insulating to better than code minimum, and using an efficient structural design to work in tandem with HVAC equipment placement and eliminate otherwise unnecessary structural support.
We’re proud of our design-build process here at A.C.E., and we encourage you to check out our design-build service page to learn a little more about us!
4. Natural Lighting
Natural lighting is something that was once a given. Any historical images of early manufacturing facilities will show large expanses of windows and skylights. When energy conservation became a significant factor in operational costs and code restrictions, the paradigm shifted to spaces with little or, in some cases, zero natural light.
However, the advancements in window and glass technology have caused the pendulum to swing in the other direction. We can now design spaces that meet or exceed code, are energy efficient, and provide natural light.
Natural light and views of the outdoors are incredibly beneficial for an individual’s psyche. When was the last time you sat in a dental chair that didn’t have a window looking outdoors? Think that’s a coincidence? It’s not - because it’s calming!
What Can Go Wrong?
This question should actually be, “What can go right?” Studies show that people are more efficient, have better attitudes, and are overall happier working in environments with natural lighting or views to the outdoors compared to those working in environments without.
According to employees and health officials, this article by Harvard Business Review claims that natural light is the number one office perk. In fact, the article states how natural light work environments reported a 51% drop in eyestrain, a 63% drop in headaches, and a 56% reduction in drowsiness.
So what comes from happier, more efficient employees within your naturally-lit facility? More productivity from less fatigue and, not to mention, less turnover.
How Can A.C.E. Help?
A.C.E. can integrate elements such as windows, light tubes, skylights, or other daylighting measures into the building’s overall design. Butler Manufacturing, our pre-engineered metal materials partner, has a skylight system that integrates directly with the MR-24® standing seam roof for assurance that the skylights won’t become a maintenance issue in the future.
5. Employee Enrichment Areas
These spaces can be traditional or contemporary - whatever vibes with your organization’s culture. However, if at all possible, these spaces’ designs should incorporate natural light or windows and access to conveniences such as Wi-Fi, device charging stations, or even fitness areas.
What Can Go Wrong?
Again, the same concept as the others above; what you could be asking is, “What can go right?” Offering more or better amenities can better position a company to attract and retain talent and deliver a better overall work environment for your employees.
How Can A.C.E. Help?
With our design-build process and previous project experience, we can help clients develop the perfect spaces for their employees.
Take a look at a few of our resources for more information on:
- The Future of Buildings, for designing with your employees in mind in 2021 and beyond.
- Is There a Building Maintenance Project Too Small? Not for A.C.E. Whether it’s adding in windows or renovating your space to add a breakroom, we’ll answer the call and do it right.
- Don't Put Off Maintenance Repairs to Your Building. Talk to our experts about OSHA and ADA compliance updates benefiting your facility and employees.
Don’t Cut Corners for Your Building’s Future Growth Potential
As crucial as it is for your project to be designed for today’s needs, you should also keep the future top of mind. Designing a space for anticipated growth can eliminate wasted construction dollars down the road for the rework or redesign of areas.
6. Design for the Future
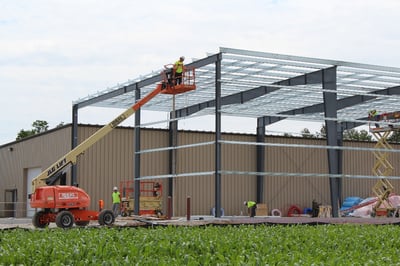
POP QUIZ!
Q: How do you appropriately position your new building on your site?
A: Pick a location to accommodate future expansion!
Did you get it right?
Here are a few additional ways that people should design their manufacturing building to accommodate the future:
- Infrastructure! Short-sighting an electrical service size can happen if you don’t properly plan for future needs. Extend the sanitary sewer to the outer edge of the building, which accommodates future plumbing needs. And finally, use technology that isn’t nearing the end of its relevance because of lesser installed costs.
- Design spaces that are easily flexible or transition to different uses. In other words, be prepared for your hotel to also work as a hospital. Today’s equipment and assembly processes might be tomorrow’s archaic way of doing things. Design a space that is flexible, has appropriate eave height, and minimal interior columns to work around.
- Operational costs over time. If a space can be designed to save a certain amount of labor hours per year, those savings will continue to compound and could wind up saving someone a significant amount of operational expenses.
What Can Go Wrong?
Extra costs, for starters. You may end up spending more money per square ft. if you need to expand without having the capacity for future growth already built into the design. For example, the cost of a 20,000 square ft. building today will be far less than the total of a 15,000 square ft. building today and adding on 5,000 square ft. in two years.
Fixed costs such as permitting, site work, mobilization, engineering, and architectural fees, and project management, are in effect duplicated by having two or more projects that could have been constructed with just one.
Loss of ROI. Suppose you incorporate materials nearing the end of their relevance when new materials or technology are available but only slightly more expensive. In that case, this may hurt you financially in the future. This was seen in previous years when LED lighting was gaining popularity. People that chose high-efficiency fluorescent lighting found themselves upgrading to LED in a matter of only a few years because they could save significant operating expenses with lower utility bills.
How Can A.C.E. Help?
At A.C.E., we keep up-to-date on building trends and design ideas through webinars, design literature, product innovations, and strategic partnerships with design professionals and building trade professionals.
Our partnership with Butler Manufacturing keeps us at the forefront of pre-engineered metal building and systems construction innovation. Butler is the industry leader in the development of new products and offerings with systems construction.
Read one of our latest articles about the future of buildings for designing with your future in mind for 2021 and beyond.
Not Sure Where to Begin? Give Us a Call!
A.C.E. is here to help you optimally design your new manufacturing facility or facility expansion. We design and build with your timeline, budget, employees, integrity, and future in mind!
Our customers will attest that our ability to listen carefully to their needs has kept them coming back to A.C.E. as their preferred general contractor. Integrity, trust, fairness, honesty, reliability, responsiveness, and respect—these are the qualities to which we remain true.
Are you interested in learning more about our services or our partnership with Butler Manufacturing? Call us today or complete the project consultation form! We look forward to hearing from you!