Different building types have unique requirements for their exterior wall systems. The wall system for an office building will differ significantly from that of a food packing facility, warehouse, school, or church. Even two buildings with similar frameworks can vary in functionality, appearance, and cost based on their exterior cladding or wall systems.
This article explains how various construction wall systems work, what benefits each type offers, and how to choose the best option for your building. Plus, it explores Butler Manufacturing’s pre-engineered metal wall systems, a reliable choice for many construction projects.
Building Wall Systems
Wall systems—whether tilt-up concrete panels, stud frame, or pre-engineered metal—serve specific purposes. Can a single wall system work for multiple building types? Can different systems suit one end-use? Read on to find out, and debunk common misconceptions about these systems.
Concrete Wall Systems: Tilt-Up & Precast vs. Block
One of the increasingly popular types of construction wall systems is concrete walls. They go by many names and have just a few variances. “Tilt-up” is a construction technique that sees concrete wall sections cast horizontally on the project site and precast uses concrete panels that have been cast and cured at an offsite manufacturing facility. Both types are "tilted" vertically upwards with a crane and propped into position until the remaining building components—such as the roof, floors, and walls—are secured.
Then the panels are welded at the top and bottom. Once secured, these panels become the exterior walls and can feature different textures and finishes like smooth, exposed aggregate, or decorative brick/stone patterns.
With tilt-up or precast, you’ll need a steel structure on the inside because the concrete cannot support itself on its own. The same holds true for block wall systems.
Common Uses For Structural Concrete
Many food production facilities, like cheese factories, meatpacking plants, or any new food processing facility are commonly constructed from tilt-up concrete wall systems. This type of building construction is also used in areas with strict architectural protective covenants and can also be used in areas that have wet conditions.
Stud Frame & Exterior Siding Wall Systems
Stud frames and exterior siding is what most people would classify as conventional construction and is what most houses or multi-family structures are constructed out of as well as small commercial buildings like fast-food restaurants, small professional offices, and smaller commercial service structures. You can put any common exterior finishings over wood as well as pre-engineered buildings, which you will learn more about below.
Common Uses For Stud Frame & Exterior Siding
Two of the main advantages of traditional stud frame and exterior siding are cost efficiency and exterior finish customization options. National companies that have small buildings (think fast-food restaurants, professional offices, wireless service providers, etc.) often use the exterior design of their building as an extension of their branding and marketing, and just about any exterior finish can be used with this construction system. From masonry to vinyl, composite panels to fiber cement, and even wood siding, there are many options to choose from.
Many national retail or commercial chains are turning to EIFS (Exterior Insulated Finish System), often called stucco, for their exterior cladding of choice. EIFS takes paint well and can be modified easily with exterior finishes.
Pre-Engineered Metal Wall Systems vs. Conventional Metal Wall Systems
Pre-engineered steel systems were introduced around the era of World War II. Have you ever heard of something called a Quonset hut? You've probably seen one before driving through the countryside. They usually look like a metal half-dome or barrel roof building who’s curved walls extend all the way to the ground. Kits for these metal huts were used in the military for offices and MASH (Mobile Army Surgical Hospital) units because you could build them very quickly. Companies, such as Butler Manufacturing, saw that the military could set up new barracks or other buildings in a matter of days and thought, “We could probably do this for other structures just as fast and easily.”
So what’s the difference between pre-engineered metal buildings and conventional metal buildings? There are a few distinctions but it boils down to time and cost.
When you go to a home improvement store, you can find wood in two by sixes, two by eights, two by tens, two by twelves, etc. You can't go to the store and get a two by five and a half; you’ll only be able to find the two by four or two by six. The same thing goes for regular steel. There are certain widths, depths, and heights.
Building with conventional steel requires lots of engineering that needs to be performed before the cost of the project is realized. The conventional process involves an engineer that looks at the properties of each piece of steel and checks to see if it passes the engineering process for wind loads, seismic loads, and building code restrictions to ensure that the design is structurally sound. Typically these structures have more steel in them pound for pound than a pre-engineered building. This can lead to higher construction costs along with steep engineering fees—the engineering costs for a building can be well over $20,000!
When working with a design-build contractor for a pre-engineered solution, they can tell you what the structure will cost before you buy it. Therefore, the engineering is done for you ahead of time and you pay for it on the back end when you realize the total cost of your project - not the front end before you know if you will even meet your budget.
Ready to hire some outside help? Learn what to look for when choosing a general contractor!
Wall System Considerations & Needs
Different building projects have different goals and needs, along with different wall system features that you may have to consider.
Read on to find out which wall system would work best for you.
Expansion & Retrofit Wall Systems
Have you ever seen a building that looks like half of it was built in the 1970s and the other half was built yesterday? This tends to create visual dissonance and makes your new expansion or renovation look like an afterthought rather than a complete, thought-out project.
Unfortunately, it’s common to start an expansion project only to realize that the materials you initially used are no longer made and finding a perfect match would be close to impossible.
For example, say you’re renovating a 20-year-old building whose exterior wall system is brick. You want to add on but that brick isn't made anymore…now what? When dealing with a situation like this, it’s smart to bring in new wall materials and thoughtfully incorporate them into the renovation design so that the change in material looks intentional.
Find tips and tricks for a successful expansion project in this blog post!
Functional Wall Systems
Another consideration when deciding what type of wall system is best for your building project is its function. Ask yourself:
- Will your walls need to provide specific functions for your business?
- Do your interior walls need to meet certain cleanliness or strength standards?
- Do your walls play a role in keeping the assets inside your building at exact temperatures?
All food production facilities have to comply with FDA, USDA, or other regulatory guidelines, along with sanitation processes that ultimately keep people like you and me safe. When you have to sanitize facilities on a daily basis, or sometimes several times a day, your walls may have to be able to withstand wash downs and harsh cleaning agents.
In cases like these, wall systems made from tilt-up or precast concrete panels are typically used. The reason people choose a wall system like concrete or masonry is that it's very durable, even with an abundance of sanitation cycles. Metal wall systems are also suitable for these uses in many cases as well.
On the other hand, if you’re building a warehouse or storage unit, it might make more sense for you to choose a more cost-effective wall system Warehousing and storage are competitive businesses, therefore, it’s smart to build these facilities as cost-effectively as you can to maximize your return on investment
In these cases, a metal wall system panel will almost always be the best option. It's inexpensive, readily available, easy to adapt for future expansions, durable, and easy to maintain.
Trying to keep your total construction costs down? Find out how to save money on your doors.
Design-Focussed Wall Systems
Architectural appeal doesn’t just matter for projects like schools, churches, or office spaces, and it doesn’t have to cost an arm and a leg. Cost-effective metal systems can still achieve aesthetic goals through enhancements or zoning-compliant finishes, like masonry, EIFS, and decorative panels.
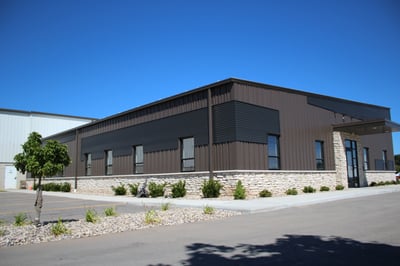
In many cases manufacturing and warehouse buildings usually want to use the most cost effective building solution. However, sometimes people want to enhance the office portion of their building or add some architectural design elements to the outside.
Sometimes local zoning codes also require some sort of architectural enhancement. The good news is that there are ways that you can make pre-engineered metal buildings look visually interesting without sacrificing cost!
Take the next step! Find out how much pre-engineered metal buildings typically cost.
Butler® Steel Building Wall Systems
Designed to complement Butler® structural systems, Butler wall systems include a variety of styles and finishes. Superior engineering delivers greater energy efficiency and fast, accurate installation. Read on for the benefits and uses of Butler wall systems:
Style 1: Butlerib® II Wall System
The Butlerib® II wall system provides both the look and performance you desire with incredible affordability. It offers unlimited design freedom and is the fundamental wall system for any Butler building. It can be incorporated with other materials such as brick, EIFS, and other Butler metal wall systems.
The Butlerib is a low-cost system that easily integrates with other metal panels, even ones built 20 or 30 years ago, and it’s easy to find everywhere
Benefits & Considerations
The Buterib wall system can accommodate up to four inches of insulation and has a variety of options for fasteners that will meet your aesthetic and security requirements.
Ideal uses for this type of wall system include:
- Large-Scale Warehouses
- Small Retail Centers
- Industrial Facilities
Style 2: Butler Thermawall™ Fluted, Fineline And Flat Wall Systems
The Butler Thermawall™ wall system creates an attractive, uniform appearance. It’s a factory-insulated wall system with hidden fasteners with R-values ranging from R-16 to R-32. Its visually appealing interior metal panel provides a finished look without the need for additional materials.
Benefits & Considerations
The Thermawall panel has metal skin on each side with insulation in the middle. Just like the tilt-up concrete panels mentioned above, it doubles as not only the wall system panel but the finished surface. It installs quickly and has a clean appearance inside and out.
We’ve used Thermawall many times for clean areas and various end uses in the food industry.
Other ideal uses for this type of wall system include:
- Commercial Facilities
- Industrial Facilities
- Architectural Applications
- Cold Storage Facilities
Style 3: eStylWall™ II Flat & Fluted Wall System
This system creates an impressive visual exterior while elevating the energy efficiency of a building’s interior.
It features a patented design using both thermal spacer blocks and fiberglass insulation with a vapor barrier that can attain R-values up to R-19.6.
Benefits & Considerations
The eStylWall™ II Flat & Fluted Wall System panel is comparable to the Thermawall™, where the fasteners are hidden. This gives it a flat appearance on the front of the building instead of having corrugations making it more architecturally appealing.
Ideal uses for this type of wall system include:
- Community Facilities
- Industrial Facilities
- Commercial Facilities
Style 4: TextureWall™ Panel Wall System
The Butler TextureWall™ panel system is a factory-insulated metal wall system with interlocking panels that resist the effects of impact, abrasion, and weather.
Benefits & Considerations
The interior panel face is finished in a fine line configuration with a polyester white color that can stand alone or be used to apply other conventional wall materials.
The TextureWall is similar to the Thermawall in that it has insulation between two pieces of metal. The difference here is that the TextureWall has a stucco-like appearance. A lot of times city officials will ban metal buildings, but they’ll make an exception for products like TextureWall.
Protective covenants can include ordinances saying 25% of the main building face needs to be glass, stone, masonry, or architectural panel. In these cases, the goal is to move away from having plain old “metal boxes” to enhance the appearance of the area. Luckily, Butler provides several suitable solutions.
Ideal uses for this type of wall system include:
- Churches
- Community Centers
- Recreational Facilities
Style 5: Shadowall Metal Wall Panel System & Shadowall EX Metal Wall Panel System
These systems are designed for energy performance while offering long-term aesthetic and structural benefits for industrial and commercial buildings.
Benefits & Considerations
The Shadowall EX Metal Wall Panel System has a stanchion design that accommodates up to eight inches of blanket insulation, achieving remarkable U-factor ratings between 0.046 and 0.047. It provides great energy efficiency at a more affordable cost than traditional insulated metal panels, helping your building meet evolving energy codes with ease.
The Shadowall Metal Wall Panel System shares many of the same features and benefits, with a design focused on architectural appeal. It supports six inches of blanket insulation, enhancing both the thermal performance and visual appearance of your facility's exterior.
Ideal uses for this type of wall system include:
- Warehouse and Distribution Centers
- Manufacturing Plants
- Office Complexes
A.C.E. Is Your Butler Builder for Pre-Engineered Metal Wall Systems
When a metal building is the best option for our customers, A.C.E. Building Service always recommends Butler’s pre-engineered metal wall systems. Throughout every stage of construction and over the entire lifetime of the building, our clients enjoy the time- and money-saving solutions that come from using our design-build services alongside the Butler Building System.
The benefits of using Butler’s systems are numerous and so are the advantages of working with A.C.E. Building Service as your turnkey provider of building construction.
Choosing the best building wall system is important. But it’s not a decision you have to make alone. Contact A.C.E. Building Service today to learn more about our services and our partnership with Butler Manufacturing. We look forward to hearing from you!